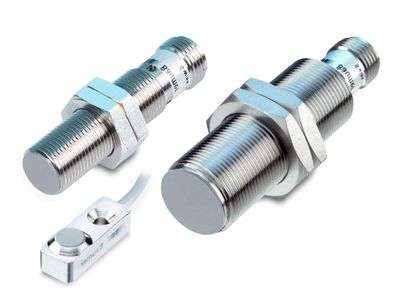
Inductive Sensors
Inductive sensors are a type of proximity sensor used extensively in industrial automation for non-contact detection of metallic objects. They operate based on the principle of electromagnetic induction, detecting changes in the magnetic field when a metal object approaches the sensor’s active area. This makes them ideal for applications requiring accurate detection without physical contact, such as assembly lines, packaging, and material handling systems.
One of the key advantages of inductive sensors is their reliability and durability in harsh environments. They are resistant to dirt, dust, oil, and vibrations, making them suitable for industries like manufacturing, automotive, and food processing. Since they do not rely on physical contact, they experience less wear and tear, which reduces maintenance needs and increases operational longevity.
Inductive sensors are also valued for their precision. They can detect metallic objects with high accuracy, even in challenging conditions where traditional mechanical sensors might fail. With fast response times, they can monitor high-speed processes, ensuring that automated systems operate smoothly and efficiently. The detection range of an inductive sensor typically depends on the size of the sensor and the metal target, with larger sensors having longer detection distances.
In industrial automation, inductive sensors are commonly used for position sensing, object detection, and machine safety. They are often integrated into systems to detect the presence or absence of parts, verify proper alignment, or monitor machine components’ position in real time.
In conclusion, inductive sensors are essential components in modern industrial automation. Their robustness, precision, and ability to function in tough environments make them invaluable for ensuring accurate, efficient, and reliable automated processes.