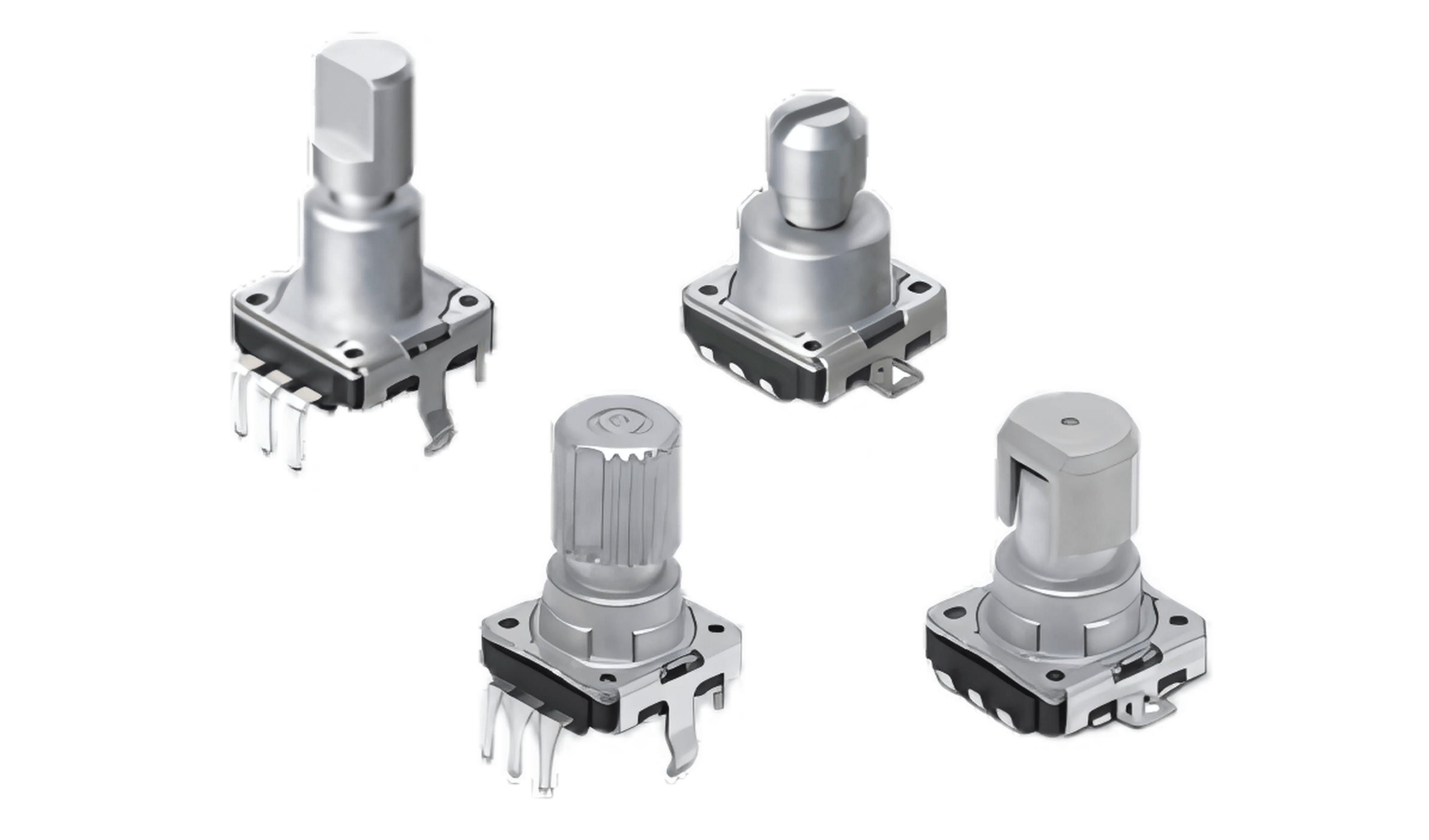
Encoders
Encoders are precision devices used to convert motion into an electrical signal that can be interpreted by control systems in various industrial and automation applications. They play a critical role in providing accurate position, speed, and direction feedback in systems like robotics, CNC machines, conveyor systems, and more. By translating mechanical movement into digital or analog signals, encoders enable precise control and automation of complex machinery.
There are two primary types of encoders: rotary and linear. Rotary encoders measure the rotation of a shaft, making them ideal for applications where angular movement or speed needs to be monitored, such as in motors or robotic arms. Linear encoders, on the other hand, measure linear displacement and are often used in machinery requiring accurate positioning, such as in manufacturing or material handling systems.
Encoders can be either incremental or absolute. Incremental encoders generate signals relative to their last position, meaning they reset upon power loss. They are commonly used in applications where speed and direction monitoring are critical, like in motor feedback systems. Absolute encoders, however, provide a unique code for every position, ensuring that even after a power loss, the system can recall the exact position of the object being measured, making them invaluable for applications where precise positioning is crucial, such as in robotics or aerospace.
The integration of encoders into automation systems leads to enhanced performance, allowing for smoother operations, reduced errors, and improved efficiency. As industries increasingly rely on automation and precision control, the role of encoders will continue to grow, becoming a foundational component in advanced manufacturing and industrial processes.